Earlier this year, I worked with a Production Manager to implement a cost savings Purge Program. The bulk of what this custom injection molding plant runs is a higher melt flow Polypropylene (PP), making both scoops and buckets in about twenty different colors. Whenever transitioning from black and moving into a lighter color, this plant routinely lost a full 8-hour shift scrapping hundreds of unsellable parts due to color streaking.
His battle was cleaning and thoroughly removing all the black colorant out from the entire system, especially the stubborn colorant stuck within the low-pressure areas of the channels and gates of hot runner manifold. His simple goal was to expedite color changes and complete them in a more reasonable amount of time. Understandably, the economics of wasting eight hours of grinding through one color change was cost-prohibitive and not a viable option. It was even more problematic since they wanted to perform 4 color changes per day on this press.
Initially, he tried using a liquid-type purging compound blended with this PP production resin to confront and facilitate his color change challenge. He reported, “This liquid purge didn't even touch the black colorant. The black still had not been cleaned after 150 shots.” This purging method was a waste of time and material.
After an quick and easy free consultation, we both believed the mass of the colorant seemed to be hung up and primarily coming from within the hot runner manifold system. The color streaking was heavier and worse in one of the cavities.
For this application, I recommended 4 Tips on Hot Runner Cleaning:
- Use a heat-activated, chemical purging compound. In this case, I recommended Asaclean NCR since it was an ideal viscosity match. Not only did it need to clean the system, it also needed to clear from the system well.
- Elevate the all heats zones of the barrel and screw, nozzle, hot runner and the tips of drops to whatever he was willing and able to get to and put him in a good position to generate prime chemical activity. This topic was recently covered in my colleague Chris Melchiore's last blog post. Chris is one of the industry’s leading experts in chemical purges and the article is a great read.
- First, use a short heat soak at elevated heats to isolate, target, and clean the barrel and screw. Then use an additional brief heat soak to isolate, target, and clean the hot runner manifold. In this case, I felt it was better to do it sequentially, instead of simultaneously. I realize in other cases, it’s better to do it simultaneously, instead of sequentially. Check with a purging expert for a recommendation.
- After the two heat soaks with the NCR, empty it out of the system by shooting parts with his production resin, bring down all temperatures for this PP resin and resume making parts.
The Production Manager reported the NCR worked well and was impressed with the performance after the first trial. He expediated his color change, going from a black to light yellow, in about an hour on a 750T press. By using about $76 worth of NCR, his Cost Purge Purge was reduced by 80%. Do you grapple with hot runner cleaning? If so, this is a very good option to cut down your scrap.
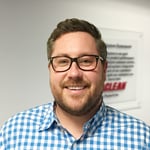
Ben Moore brings over 20 years of experience as a Purging Expert at Asaclean Purging Compounds, a leading manufacturer and distributor of purging compounds. As part of Asahi Kasei Plastics North America, Inc. (APNA), Ben has personally assisted hundreds of customers, helping them achieve significant cost savings. Based in Parsippany, NJ, Ben specializes in optimizing operations for thermoplastic injection molding, extrusion, compounding, and blow molding processes. His expertise lies in maximizing production efficiency by minimizing downtime and reducing scrap. For those interested in trying Asaclean products or seeking expert guidance, feel free to contact Ben directly. You can contact him at 800-787-4348, extension 227, or via email at bmoore@asaclean.com.
Comments