I have recently heard from a few customers, who have been using our mechanical purge compounds, that the purge is doing a great job at cleaning the screw and barrel, but they have issues in other areas i.e. the die and/or the hot runner manifolds.
One particular customer extruding PVC, reported that after purging they had a lot of issues with clogging at the die, which would require manual cleaning.
This was not only time consuming, but required a lot of effort, and the processors were not happy.
Given the nature of the resin and the equipment, the extruder had a temperature limit of 380F and also a limit on the screw speed, causing the machine to cut off once a given pressure limit was reached.
When using a mechanical purge cleaning power is dependent upon the mechanical properties of the purge inside the machine. The purge is assisted by a high pressure environment, and turbulence is usually created by increasing screw speed. In this case, screw speed was limited however a lower processing temperature (360F) was benefiting the mechanical purge.
At low temperatures, a higher viscosity provides the purge with more effective scrubbing power, however when the purge moves into a smaller region, i.e. the die, the viscosity then becomes an issue and causes clogging.
To overcome this, viscosity can be reduced by increasing temperatures, allowing the purge to flow more freely in tight areas. However, a temperature limitation meant this was not possible leaving us unable to relieve the clogging at the die head.
We decided to try a chemical purge.
Unlike a mechanical purge, a chemical purge works by heat and containment. The system was first flushed clean, and the chemical purge was allowed to enter and sit in the barrel at the maximum temperature, 380F (hopper to die) for a 15-minute soak time.
The chemical purge worked well and was able to remove contamination from the die, without clogging it up. In stubborn cases a second purge was required (usually the second purge at an elevated temperature will give more effective results- however the purge still provided effective cleaning at 380F). The processors were very pleased with the result.
Similarly, another customer was experiencing 6+ hours downtime on their injection molding machine, when carrying out a color change, due to a hang up of color in the manifolds.
A hot runner safe mechanical purge was recommended, which again was great for cleaning the screw and barrel, but even at elevated temperatures (500F), was still experiencing difficulty in pushing through the hot runners, and was clogging up at the nozzle.
Again, we decided to try a chemical purge, a first purge at 380F with a 15-minute soak, and second purge at 410F again with a 15-minute soak time, and we saw great results.
The purge was able to effectively clean the hot runner manifolds without clogging, and even with the added soak times it was much less time consuming than taking the machine apart OR running hundreds of scrap parts. The customer was able to reduce the downtime required to manually clean the die and hot runners from 6 hours to 1.5 hours.
Although a mechanical purge can be great for cleaning the screw and barrel, and is very easy to use(allowing you to go straight in and out from one production resin to the next), sometimes spending a little more time on your purge process, and using a chemical purge can give you the edge needed to clean those hard to reach areas.
Learn how to reduce machine downtime with five quick purging compound tips for your injection molding application.
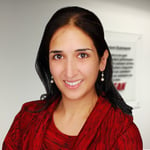
Kiran Raza is an Asaclean Purging Expert & Technical Sales Representative. She's worked in the plastics industry for nearly 20 years and has expertise In Bio-Medical Materials, Polymer Processing, and Materials Testing.
Comments